Fasteners are the most widely used products in all industries. They appear in any industry. Billions of fasteners are consumed every day. More than 2,000 fasteners are used in a single car. So what are the processing methods for these fasteners? What materials are used in each method?
The general fastener processing process is:
(Incoming raw material inspection) Pan Yuan – Annealing – Pickling – Phosphating – Saponification – Drawing – Cold heading – Turning – Tooth making and thread rolling) – Heat treatment – Surface treatment – Final inspection – Packaging – Shipping and transportation – deliver
(Annealing-pickling-phosphating-saponification-drawing) is the material transformation stage
Cold heading – turning – thread making (thread rolling, thread rolling) is the blank forming stage
1. Cold heading processing

This method mainly processes bolts, screws, nuts, rivets and pins, and the processing equipment used is a cold heading machine. The production efficiency of this process is very high, generally 120 pieces/minute, and high-speed equipment can reach more than 300. Due to its high processing efficiency, more than 95% of bolt products on the market are processed through this process. Commonly used cold heading The machines include: double-click cold heading machine, open and close mold cold heading machine, multi-station cold heading machine, ultra-high-speed multi-station cold heading machine.

This process is to use the plastic deformation of the material at room temperature to finally shape the round wire into a cold heading blank, and then go through processes such as wire rolling, heat treatment, and surface treatment to make the final product. Since the processing environment is at room temperature, materials with better plasticity properties must be selected. Cold heading parts use special rivet materials for cold heading (the material grade is preceded by ML, such as ML35). This type of material is generally used in Appropriately increase or decrease the proportion of chemical components in the basic brand. Basically all steel mills produce this type of material, and then add a phosphating film to the material after modification, and it becomes a special material for cold heading.
1.1 Advantages of this process:
- High production efficiency, suitable for large batches;
- High material utilization rate, except that some products will be trimmed and punched, basically no waste will be produced;
- Because the bolts will not be further machined After processing, the product has complete metal streamlines and excellent mechanical properties and fatigue properties.
1.2 Disadvantages:
- Parts with more complex structures require the use of multi-station cold heading machines. Multi-station cold heading machines are more expensive and require larger equipment investments;
- The price of forming molds is higher than other processes; 3. Unable to process specifications. Large and long length pieces.
2. Hot forging
This method mainly processes bolts and pins, and the equipment used includes punches and hydraulic presses. The production efficiency of this process is low. Because the material will be heated before molding, causing oxidation of the surface layer, the exposed parts after molding will be very ugly. Therefore, machining procedures are generally used to process the working surface to meet the usage requirements.
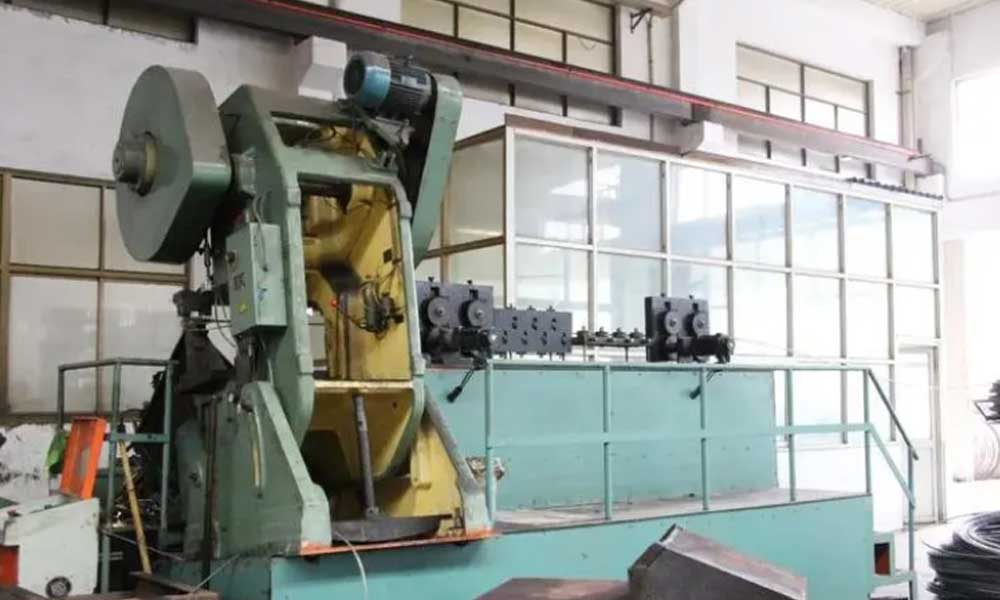
This process softens the material by heating it to high temperatures, and then plastically molds it in the mold cavity. Most existing materials will soften after high temperatures and can eventually be processed and formed. Therefore, as long as the materials used in this process can meet the design mechanical performance requirements after heat treatment, no special treatment is required for the materials.
2.1 Advantages of this process:
- It can process parts with large specifications and long lengths;
- Low equipment investment.
2.2 Disadvantages:
- Low production efficiency;
- Poor appearance, often uneven;
- The forged blank has large tolerances and many burrs, so it must be processed with machining procedures; 4. It can only be processed with a simple structure Parts, processing complex parts can only add more steps.
3. Machining
This method is relatively barbaric. It is processed directly through turning, milling, drilling, cutting and other machining methods, and the processing efficiency is very low.
The materials used in this process can be processed as long as their properties after heat treatment meet the requirements.
3.1 Advantages of this process:
- The dimensional tolerances of the processed parts can be optimized, so this process can be used for some parts that require extremely high tolerances, such as screws used for human bone correction;
- Because the equipment used is easy to obtain , so it can be used to process manual prototypes with smaller quantity requirements.
3.2 Disadvantages:
- The efficiency is extremely low, which is very unfavorable for mass production;
- The processing cost is high.
Fastener processing is a complex and critical process, which directly affects the quality and performance of the product. During the processing, we need to reasonably select materials, strictly control the processing technology, and conduct quality control to ensure that the product meets the design requirements. By continuously improving and optimizing the process, we are able to improve the quality and production efficiency of fasteners and meet the needs of the market.